Your smartphone begins life neatly packed into a well-designed box. Chances are it will end its days in a more ignominious manner.
Assuming it doesn’t end up rattling around in a junk drawer, it will most likely go to the same landfill as your other household waste, where it will slowly leach toxic chemicals into the soil and water. Or worse, it might be shipped to another country, where low-income workers will manually break the phone apart to recover anything of value and burn or bury the rest, putting their health—and that of their wider community—at risk in the process. Meanwhile, miners continue to plunder Earth for metals and minerals to feed our unquenchable hunger for new gadgets.
The problem posed by electronic waste, or e-waste, is only getting larger. “It’s the fastest growing waste stream,” says Pablo Dias, an engineer specializing in management of e-waste at the University of New South Wales in Sydney, Australia. According to the Global E-waste Monitor, a project backed by the United Nations Institute for Training and Research, people disposed of 53.6 million metric tonnes of e-waste in 2019—a quantity that is expected to increase by nearly 40% by 20301.
On supporting science journalism
If you're enjoying this article, consider supporting our award-winning journalism by subscribing. By purchasing a subscription you are helping to ensure the future of impactful stories about the discoveries and ideas shaping our world today.
Oladele Ogunseitan, a public-health researcher at the University of California, Irvine, thinks things are starting to change. “We are making enough noise that the manufacturers are not able to ignore it anymore,” he says. And there are ample opportunities to circularize the electronics industry. The precious and scarce metals these devices contain can be reused near-indefinitely, and emerging technologies that make their recovery easier could drastically reduce the need for mining. Parallel progress in recyclable and biodegradable circuit boards could eliminate the more toxic ingredients in electronics and allow consumers to bin defunct devices without guilt.
“This is an opportunity to stop thinking of it as waste,” says Clara Santato, a chemist specializing in electroactive materials at Polytechnique Montréal in Canada. But making electronics more sustainable will also require a more radical evolution of the industry as a whole, as well as the consumers who crave their products.
Swept under the carpet
E-waste is a category that comprises a diverse array of electrical equipment, for which the material can vary as much as their form and function. One estimate suggests that as many as 69 different chemical elements might be found in e-waste1. “We looked at 10 different smartphone printed circuit boards, and found that the variation in material content was quite significant,” says Jeff Kettle, an electronics engineer at the University of Glasgow, UK.
Standard building blocks such as silicon, iron and copper are typically joined by more exotic elements. These include highly conductive precious metals such as platinum and gold, as well as rare-earth elements such as neodymium, which possess unique magnetic and electrical properties. Although not geologically rare, these elements are logistically difficult to obtain and mainly sourced from just a few countries—most notably, China. Some devices also contain heavy metals such as lead and cadmium that seriously threaten human and environmental health.
E-waste contains these hard-to-find elements in abundance. If the useful materials can be efficiently separated from those that are not, then waste could become a gold mine, both literally and figuratively. “When you find rare-earths in ores, they come in parts per million—when you have them in magnets, they come in percentages,” says Ikenna Nlebedim, a materials scientist at the Ames National Laboratory in Iowa. The quality of these recovered elements is also assured: they have already been deemed suitable for use in electronics. Similarly, estimates suggest that precious metals might be up to 50 times more abundant in e-waste than in mined ores.
The Global E-waste Monitor reports that, as of 2019, only around 17% of the world’s e-waste was being properly managed for recycling in the countries that generate it1 (see ‘The digital dumping ground’). The rest is nearly impossible to account for and presumably ends up in local landfills, wasting valuable materials and inflicting lasting environmental damage. But a sizable fraction of this material is offloaded onto countries in Asia, Africa and Latin America. Robust numbers are hard to come by, but a 2016 monitoring study by the Basel Action Network, an environmental watchdog in Seattle, Washington, found that up to 40% of e-waste thought to be slated for recycling from the United States might be exported2.
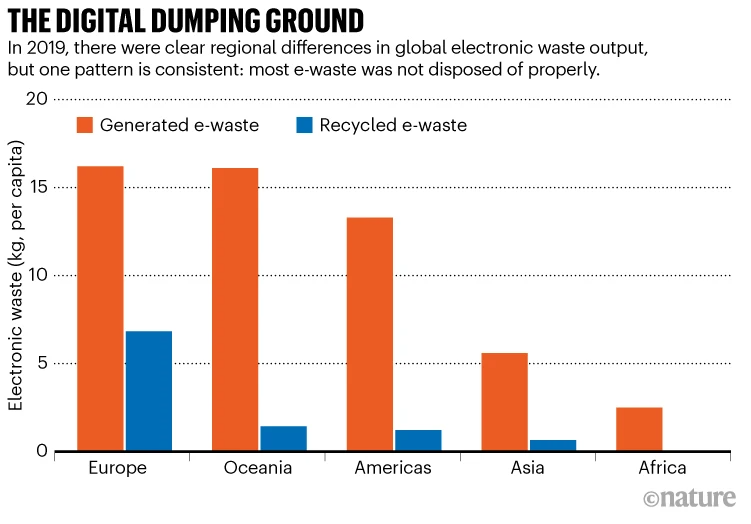
Source: The Global E-waste Statistics Partnership
Ogunseitan sees several reasons why recycling hasn’t taken off in the United States. “Economically, it’s difficult to make a big profit, but also we have a lot of environmental laws that keep out factories that would easily dismantle and smelt,” he says. Many regions also lack effective collection systems for recovering household and business e-waste. And so this waste ends up in Ghana, Vietnam, Brazil and other countries, where networks of informal recyclers manually strip shiploads of discarded electronics. E-waste export is heavily restricted by the Basel Convention, a United Nations treaty that took effect in 1992. But the United States has never ratified the convention. There are also significant loopholes—for example, some exporters misrepresent e-waste as donations.
Informal recycling has become an important, albeit dangerous, source of livelihood for some people in these countries. “People manually take out the things that are more valuable, such as printed circuit boards, hard drives and memory, and send these back to the high-income countries for further processing,” says Dias. The remainder is burned or just piled on the ground, creating a continuing public-health catastrophe. A 2012 study revealed that inhabitants of a rural e-waste processing community in China were 60% more likely to develop lung cancer than were people living in the nearby major city of Guangzhou3. This was due to inhalation of toxic-waste by-products, which are released into the air after incinerating e-waste.
Several countries have successfully pushed for change—between 2018 and 2021 China moved to reject all imported solid waste after decades of damage. But this ultimately results in the waste being directed elsewhere, and the scope of the problem remains daunting.
Ripe for recovery
A practice known as urban mining offers one solution for improving the management of e-waste and incentivizing countries to retain and process their leftovers rather than burying, burning or exporting them. This involves chemical or physical processes to separate precious metals or rare-earth elements present in e-waste from materials that are toxic or of little value.
Two approaches currently predominate in urban mining. Pyrometallurgy, in which preprocessed waste material is heated to extremely high temperatures—often upwards of 1,000 °C—to burn away plastics and other unwanted materials and yield a mixed fraction of molten precious metals that can then be purified. “The downside is that these approaches are energy intensive,” says Nlebedim. As an alternative, some facilities use strong acids to dissolve the metals present in e-waste. Although less energy intensive, Nlebedim notes that this hydrometallurgic method has its own negative environmental footprint, producing acid-laden toxic sludge and lots of waste water.
Urban-mining operations are currently active at a relatively small number of facilities worldwide. But the profit margins can be slim, which has limited the growth of this sector. “They require very big volumes to be able to be profitable, so it’s hard for another small player to come in and compete with them,” Dias says. The costs associated with urban mining—such as preprocessing, metal purification and waste management—add up quickly, potentially shifting the cost equation back in favour of traditional mining. “You can’t tell somebody, ‘Mine is recycled, pay $10 more per kilogram to buy it,’” Nlebedim says. Fortunately, methods now in development—including a few that are on the verge of commercialization—could tip the balance in favour of recycling.
For example, James Tour, a synthetic chemist at Rice University in Houston, Texas, has applied a technique known as flash Joule heating to rapid, low-cost e-waste processing. Flash Joule heating subjects materials to an intense blast of energy, bringing them to temperatures that vapourize the metals so that only carbon is left behind in the chamber. But unlike pyrometallurgy, the heating is incredibly brief—typically a few hundred milliseconds. The resulting metal vapours can then be extracted under vacuum and condensed by cooling. Flash Joule heating has a clear economic appeal: it can be performed at a cost of roughly US$12 per tonne of waste, with minimal energy and water use required.
In an initial demonstration, this method recovered more than 80% of the precious metals, such as palladium and silver, that were present in an e-waste sample4, while also enabling easy isolation of toxic compounds such as mercury and lead. “The remainder is clean enough for agricultural soil, even by California standards,” says Tour. He and his colleagues are now trying to license the technology to companies for use in urban mining of e-waste.
Nlebedim and colleagues have developed an alternative, acid-free approach to hydrometallurgy for recovering rare-earth elements in the permanent magnets that are commonly found in hard drives and motors5. The researchers identified reaction conditions in which the valuable magnetic components are selectively dissolved at neutral pH while leaving other materials intact, which means that minimal processing is required before recycling. The dissolved rare-earth elements can subsequently be purified from the solution, yielding material of sufficient quality for reuse in electronics. This technology is being commercialized by a manufacturing company called TdVib based in Boone, Iowa, which is on track to have its first pilot plant fully operational by the end of 2022. “We are currently running batches of 800 kilograms at a time and will be scaling up in the next few months to batches of about 8,000 kilograms,” TdVib chief executive Daniel Bina said in late September.
Waste not
Not everything can be readily recycled, but there are opportunities to create ‘green electronics’ that can be produced and disposed of in a more environmentally friendly way. Rodrigo Martins, a materials scientist at the New University of Lisbon, is confident that many of the functions performed by modern silicon-based devices could one day be replicated with Earth-friendly alternatives, eventually eliminating the need for scarce metals, non-biodegradable plastics or energy-intensive manufacturing.
Conventional circuit boards are built on fibreglass, which is non-biodegradable and typically laced with potentially toxic fire-retardant compounds. Martins’ group is working on paper-based boards that could offer an environmentally friendlier alternative. In 2011, Martins and his collaborator and wife, Elvira Fortunato, described a paper-based complementary metal-oxide semiconductor (CMOS) device6—a core component in modern integrated circuits. The conductive materials in this device were based on zinc oxide rather than on silicon, which is typically used, and the use of this substance or other metal oxides could greatly reduce the cost and greenhouse-gas footprint associated with manufacturing.
Martins’s team has continued to develop techniques for efficient and reproducible printing of paper-based devices, and is exploring the use of alternative materials—including combinations of graphene with common metals such as bismuth and molybdenum. He notes that as their performance improves, the devices get smaller, which confers an additional edge. “It means the amount of raw material that I’m consuming is, by far, less,” says Martins. “And I can use materials which are abundant and nontoxic.”
Other groups are exploring a variety of alternative biodegradable circuit-board components. For example, Ogunseitan and his long-time collaborator Johnny Lincoln who founded Axiom Materials, a composite-materials manufacturer in Santa Ana, California, are investigating the commercial viability of circuit boards based on flax and a linseed-oil-derived epoxy, which they first demonstrated in 20087. And Santato’s team is looking at the possibility of replacing silicon-based semiconductors with melanin, a naturally derived pigment that is capable of efficient electron transport. This year, Santato’s group has demonstrated that melanin-based films can almost match the performance of more-established organic semiconductors8. And although their current source of melanin is cuttlefish ink, Santato points out that she could obtain the substance from food waste.
This July saw the formal launch of the UK Green Energy-Optimised Printed Transient Integrated Circuits (GEOPIC) initiative, a programme led by Ravinder Dahiya at the University of Glasgow, for which Kettle is also an investigator, that brings together academic, government and industry specialists to make circuit-board production more sustainable. “GEOPIC is about developing biodegradable integrated circuits, biodegradable substrates, biodegradable interconnects and so on,” says Kettle. This will not tackle every aspect of the sustainability problem, but could lead to greener manufacturing processes and far less e-waste in the long term.
How broadly these biodegradable components might overturn the circuit board status quo in the near term remains an open question. “You do have to compromise on performance,” says Kettle. Flexible and compostable substrates such as flax or paper are inherently more susceptible to damage from moisture or heat, and devices that use them must be designed with this limitation in mind. Santato thinks that materials scientists are a long way from finding eco-friendly replacements for many scarce metals. “At the moment,” she says, “you cannot reach the conductivity of gold or platinum or palladium with organic or carbon-based conductors.”
However, recyclable or compostable electronics could become invaluable in devices intended for short-term use, or in narrow-purpose devices such as wearables or environmental sensors that don’t have to meet the same rigorous performance standards as the processors found in smartphones. From Martins’s perspective, such electronics could be useful in contexts such as monitoring water quality or food safety, or the manufacture of low-cost displays, without meaningfully adding to the planet’s e-waste burden.
Creating a culture shift
Many researchers working on the e-waste problem have been pleasantly surprised to find enthusiastic partners in the commercial sector. For example, Ogunseitan is conducting research funded by Microsoft, and Tour says he is in regular contact with companies looking to minimize the impact associated with keeping their IT infrastructure current. “Server farms are changing over every three years, and you get mountains of printed circuit boards,” Tour says. These facilities “don’t know what to do with all of this toxic waste”, he explains.
But more-aggressive measures will probably be necessary, including tighter regulations. Dias thinks that strict bans on landfill deposition of e-waste is a crucial first step. “The biggest competitor for recycling is landfill,” he says. With this option off the table, the competition will shift to delivering the most cost-effective recycling service. Dias further emphasizes that this step must also be coupled with more-stringent monitoring and enforcement of export restrictions to prevent a massive surge of e-waste from high-income nations onto the shores of lower-income countries.
Manufacturers should also pursue practices that promote circularity. “There needs to be a very clear policy for ‘end of life’, where the producer takes back the product,” says Santato. A few device manufacturers are already doing this; for example, Amsterdam-based smartphone manufacturer Fairphone reported having recycled as many phones in 2021 as they have sold to consumers. Modular electronic devices designed for easy disassembly and repair could also incentivize recycling by making it easier and cheaper to break down—or service—broken or obsolete devices.
But consumers will also need to play their part—particularly in high-income countries, where it is more routine to replace high-end electronic devices such as smartphones every few years. “We often think of recycling as this silver bullet—it’s not,” says Dias. “Reducing should be the overarching goal.” Planned obsolescence by manufacturers is part of the problem, but resolving this issue will also be a matter of public education and policies that boost civic-mindedness and environmental consciousness. “We can have an amazing device that lasts four or five years and still have a good life,” says Dias. “We’re not going to have to give up as much as we think we will.”
This article is part of Nature Outlook: Circular Economy, an editorially independent supplement produced with financial support from Google. About this content.
References
Forti, V., Baldé, C. P., Kuehr, R. & Bel, G. The Global E-waste Monitor 2020 (UNU/UNITAR, ITU & ISWA, 2020).
Hopson, E. & Puckett, J. Scam Recycling: e-Dumping on Asia by US Recyclers (Basel Action Network, 2016).
Wang, J. et al. Environ. Sci. Technol. 46, 9745–9752 (2012).
Deng, B. et al. Nature Commun. 12, 5794 (2021).
Prodius, D., Gandha, K., Mudring, A.-V. & Nlebedim, I. C. ACS Sustainable Chem. Eng. 8, 1455–1463 (2020).
Martins, R. et al. Adv. Mater. 23, 4491–4496 (2011).
Lincoln, J. D., Shapiro, A. A., Earthman, J. C., Saphores, J.-D. M. & Ogunseitan, O. A. IEEE Trans. Electron. Packag. Manuf. 31, 211–220 (2008).
Camus, A. et al. Proc. Natl Acad. Sci. USA 119, e2200058119 (2022).